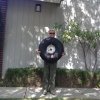
Reworking a B model cowling
Started by
C5Engineer,
62 posts in this topic
Create an account or sign in to comment
You need to be a member in order to leave a comment
Started by
C5Engineer,
You need to be a member in order to leave a comment