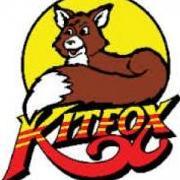
Power loss. Off field landing...
Started by
gregpro50,
83 posts in this topic
Create an account or sign in to comment
You need to be a member in order to leave a comment
Started by
gregpro50,
You need to be a member in order to leave a comment